Anti-mite technology and development of anti-mite fabric
2020-08-26 15:16:14
Anti-mite technology and development of anti-mite fabric
Anti-mite technology and development of anti-mite fabric
In the 1980s, people have been engaged in the research of fabric anti-mite antibacterial finishing. In Germany, Herst started to produce anti-caries agent MITE, and in Switzerland Santized company launched the fabric anti-caries agent Acitiguard AM87-12. In Australia, ATCP launched the anti-caries agent Healthguard. In Japan, anti-mite anti-bacterial fabrics have achieved industrial production. At the same time, Japanese merchants have processed anti-mite anti-bacterial fabrics in the form of anti-mite anti-bacterial agents in China. Some merchants require direct processing of three-piece bedding sets, antibacterial and anti-mite garments. In China, mass production of anti-caries agents and anti-mite antibacterial fabrics have been supplied to domestic and foreign markets.
There are three main types of textile anti-mite methods: one is to prevent the locusts from multiplying, such as the killing method and the trapping method. The second is not to let the locusts approach, such as the repellent method. The third is not to invade the mites, such as the blocking method. The killing method is an important preventive measure. Among them, the sun, heating, electromagnetic waves, infrared rays and the like can dry the fabric and destroy the living conditions of the mites. It will die when its water content is below 10%. Chemical killing is also important, such as the use of pyrethrum extract isobornyl, dehydroacetic acid, aromatic carbonate, diphenyl ether and the like. The trapping method is to induce the mites and then kill them. This kind of temptation is characterized by sexual attraction, temptation, spawning and pheromone attraction. The repellent method is to use a repellent, which is a substance having an odor and taste that is fearful of aphids, such as the use of a repellent phenylamide aromatic carboxylate and β-naphthol. The third method of blocking is to use dense fabrics to prevent passage of mites, and in some cases to use repellents to further enhance this blocking effect.
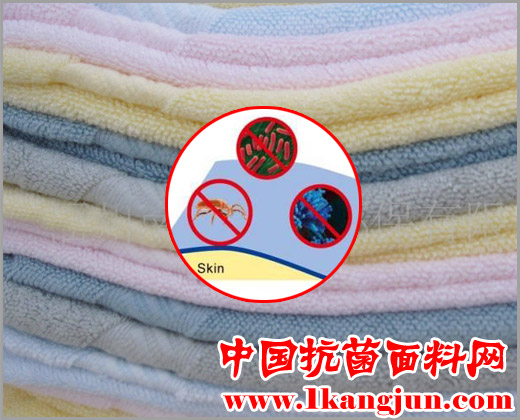
As with other functional fabrics, the techniques for imparting tamper resistance to textiles are also diverse. The methods for producing tamper resistant fabrics include functional fiber methods, fabric finishing methods, and high density fabric methods. The details are described below.
First, the functional fiber method
In this method, an anti-caries finishing agent is added to a fiber-forming polymer, and after spinning, an anti-caries fiber is produced.
By this method, the fiber material can be imparted with anti-caries properties. There are two specific methods: one is to add anti-mite finishing agent in the polymerization process of the polymer, and then to spin; the other is to make anti-mite masterbatch, and then mix with the polymer slice, in the polymer The anti-caries finishing agent is added to the fibers during the spinning process to chemically modify the fibers. Develop a method of using anti-mite fiber and anti-mite cotton.
For example, the anti-caries finishing agent SCJ-999 is mixed with a polyester polymer chip to obtain a polymer (including SCJ-999 1-3%) constituting a skin component. On the other hand, polyethylene terephthalate is used as a core component, and after being melt-spun and spun together with the polymer constituting the skin component, heat treatment is further carried out at 125 ° C for 20 minutes to obtain an anti-caries effect. Composite fiber of sheath-core structure.
Japan Bell Textile Co., Ltd. uses acrylic fiber as the substrate, and when it is in a gel state, it is coated with various anti-mite finishing agents (benzamide compound, pyrethrum, diphenyl ether or organic phosphorus) to make the anti-mite finishing agent enter the surface of the fiber. Underneath, it has improved its anti-mite. Disan Pharmaceutical Co., Ltd. produced anti-mite fibers by heat-drawing the undrawn polyester yarn after anti-mite treatment. Japan Toray Co., Ltd. has been successful in developing anti-mite materials. The anti-mite polyester fiber “Kepach-f†and the anti-mite mattress “CLINIC FUTON†are its series. The anti-caries agent used in "Kepach-f" is a mixture of a specific quaternary ammonium salt compound and a specific pyrethrum extract. The "CLINIC FUTON" developed with "Kepach-f" and high-density fabrics enjoys a high reputation in the Japanese market. Developers have published a paper on the effect of this sputum in the 25th Japan Children's Allergy Society. The study was conducted in 22 families involved in childhood asthma, using "CLINIC FUTON" bedding and 100% polyester bedding, which were tested by children and their siblings and parents. The trial was conducted in the same room. The conditions of drying and storage are the same, and picking is carried out before and after use. As a result, the number of mites on the "CLINIC FUTON" was 90% less than that of the comparative sample, which proved its mites.
In addition, it is reported that some people will graft copper ions by chemical reaction on the acrylic fiber, and attach the X-GL golden C19H24N3+O group to obtain the modified fiber and graft the acrylic fiber by chemical reaction in the same way. The copper ion and the modified fiber obtained by connecting the X-GB blue C20H24N3+O group and other fibers are mixed together, and subjected to a treatment process such as opening and laying, to obtain a non-woven fabric having a tamper-proof effect.
Now Beijing Jieer Shuang High-Tech Co., Ltd. has developed a highly effective anti-mite antibacterial agent and anti-mite antibacterial masterbatch for polypropylene and polyester fibers. The anti-mite and antibacterial double-effect anti-mite antibacterial viscose filaments were successfully developed by using the anti-caries agent SCJ-998. The fiber was tested by the Chinese Center for Disease Control and the Chinese People's Liberation Army Military Medical Research Institute and other authoritative testing institutions. Excellent anti-mite and anti-bacterial properties: the aphid repellent rate is over 99.9%, and the antibacterial rate is over 99.9%. At the same time, the fiber also has good safety, durability and post-processability.
Blend-resistant chemical fibers are often blended with natural fibers to balance the comfort and tamper resistance of natural fibers. However, the pretreatment of ordinary natural fabrics generally requires a process such as caustic soda refining, chlorine-oxygen double bleaching, and strong alkali mercerizing. Since the anti-caries finishing agent used may not be resistant to acid, alkali or oxidation, reduction, etc., the anti-caries fibers and fabrics produced therefrom have some special requirements for the dyeing and finishing process. This requires that in the dyeing and finishing process, it is necessary to consider both the anti-mite effect and the characteristics of anti-mite fiber and fabric. Otherwise, it will directly affect the anti-mite effect of the anti-mite fabric. In order to ensure the anti-mite effect of the product, it is usually treated with anti-mite antibacterial agent SCJ-998 to obtain the anti-mite and antibacterial effect.
Second, the fabric finishing method
The human body constantly produces fluid secretions in the form of sweat, oil, and skin detachment, providing the best breeding ground for organic microorganisms on the skin. The ideal environment for microbial growth between fabric and skin - moist and warm. Aphids can multiply tens of thousands without paying attention, resulting in reduced hygiene, unpleasant odors caused by microbial metabolism, and even skin infections. Textiles are generally washed at 60 ° C, and even if they are carefully washed, they look clean, but at this temperature the aphids and germs still survive. The antibacterial and anti-mite treatment agent used has an antibacterial and anti-mite effect, and deprives the aphids and bacteria of nourishing conditions, so that it cannot be propagated.
Anti-mite finishing is a process in which the fabric is treated with an anti-caries agent to provide a tamper-proof property and keep the textile clean and hygienic. Its purpose is not only to keep the fabric clean, but more importantly, to prevent infectious diseases, to ensure the safety and health of the human body and to wear comfortably, to reduce the cross-infection rate of the public environment, and to make the fabric a new function of health care. The anti-mite finishing fabric can be widely used in people's underwear, towels, bath towels, bed sheets, duvet covers, blankets, decorative fabrics, carpets, air filter materials, etc., and has great social benefits.
Fabric anti-mite finishing technology is an edge technology that combines modern medicine, fine chemicals and new dyeing and finishing technologies. The key issue is how to design and synthesize the molecular structure of the mothproofing agent from the chemical aspect; to study the effect and safety of the anti-caries agent from the medical aspect; to solve the combination of anti-caries agent and fiber from the dyeing and finishing aspect and The fastness, strength, whiteness and permeability of the fabric. The Japanese paid special attention to the issue of flood control, and began to develop anti-mite fabrics in the 1980s. Various products have been put on the market. The anti-mite fabrics developed by Toray and Toyo Textile have good results. Beijing Jieer Shuang High-Tech Co., Ltd. is the only manufacturer in China to mass produce fabric anti-caries agent. The test results of domestic authoritative testing institutions show that the fabric after anti-mite anti-bacterial finishing is non-toxic and has no allergic reaction to the skin. The repellent rate of dust mites, leather mites and mites is more than 93%, and the repellent rate of washing 50 times is more than 85%, which has obvious effects on preventing skin itching and asthma.
The anti-smashing finishing method is to post-finish the fabric with the anti-mite finishing agent to achieve the anti-caries effect. This is a conventional technique, which is sprayed, padded, coated, etc. The key to this technology is the choice of anti-caries finishing agent and the preparation of the finishing agent. The anti-caries agent is filled into the microcapsules, and the film-forming material such as resin can be bonded to the fabric, and the anti-caries agent and the organosiloxane are made into a coating liquid, which is more convenient to use. Examples of the anti-caries agent include phenylamide, naphthol-based compound isobornyl, and ethyl thiocyanate, and plant substances such as pyrethrum extract, eucalyptus oil, and persimmon.
In addition, the anti-caries finishing agent is dissolved in the "shale tar A" solvent, and the sorbic acid sol 2942S, heptane sol 100 and calcium dodecylbenzenesulfonate are used as emulsifiers, and fully stirred into a uniform anti-caries finishing agent. Emulsion. This anti-caries finishing agent emulsion is mixed with a latex liquid of a polyacrylonitrile resin, a polyester resin, and a polyurethane to obtain an anti-caries treatment liquid. The anti-caries treatment liquid is treated as follows: the cotton cloth and the polyester/cotton (65:35) blended fabric are immersed in the anti-caries treatment liquid, and dried by a rolling mill until the liquid-liquid ratio is 80%, and then at 80 ° C. It was dried for 5 minutes and finally heat treated at 130 ° C for 1 minute. After such treatment, the fiber and its fabric can be imparted with a good anti-mite effect.
It is also described that the emulsion of the isocyanurate acetate and the emulsion of the polyester copolymer can be treated in the same bath to obtain a durable anti-caries effect. The polyester interpolymer is emulsified and dispersed in water by a nonionic or anionic surfactant to form an emulsion. The isocyanurate acetate as a tamper-proof finishing agent is emulsified and dispersed in water by a nonionic or anionic surfactant to form an emulsion. The polyester fabric was heat-treated at 180 ° C for 2-4 minutes after being padded (with a liquid ratio of 80%) and dried (100 ° C) to improve the washing resistance of the anti-caries effect.
Santized Company of Switzerland developed the anti-wrinkle and anti-mite finishing process for garments. The finishing sequence is fabric garment processing, pre-treatment washing (yield washing), drying (cloth pH 6-7), impregnating anti-wrinkle liquid (pH 5±0.5), Dehydration (60-80% humidity), drying (100-110 ° C or less, 10-20% humidity), styling pressing (140 ° C 20 s), inspection before baking oven, furnace baking (145, 155 ° C × 5, 15min), cooling and packaging. Then carry out anti-mite treatment, and finally cool and package. At present, the most widely used anti-caries agent in China is SCJ-999 and anti-mite antibacterial agent SCJ-998 (Beijing Jieer Shuang High-Tech Co., Ltd.), and its application processes are:
A. Anti-caries agent SCJ-999
1. Process recipe:
Concentration (g/l) fabric
Agent
Cotton, silk, wool fabric
Polyester cotton, chemical fiber fabric
Anti-mite finishing agent SCJ-999
20-40
30-60
Low temperature fixing agent SCJ-939
20-40
30-60
2. Process flow:
Impregnation -> dehydration (the solution can be reused)
Fabric drying (70-100 ° C)
Padding finishing solution (rolling rate 70-80%)
—>Bake (140 ° C, 30 seconds, or 120 ° C, 2 minutes) -> finished product
B. Anti-mite antibacterial agent SCJ-998
The anti-caries antibacterial finishing agent SCJ-998 can be processed by padding, dipping, spraying, coating, and brushing. The amount of SCJ-998 is 3-4% owf (ie, adsorption of 3Kg to 4Kg SCJ-998 per 100Kg of dry fabric), and the specific amount is determined according to the variety and use of the treated fabric:
1. Process flow:
Fabric --> bleaching dye --> drying --> padding anti-mite anti-bacterial solution (rolling rate 70%) --> drying (80-100 ° C) --> high temperature tenter (150 ° C × 20-30 Seconds, or 120 ° C × 2-3 minutes).
2. Process formula: (taking 70% of the rolling rate as an example)
a. Domestic brand products: SCJ-998A 36 g / liter
SCJ-998B 16g / liter
SCJ-998C 8g / liter
b. Export products: SCJ-998A 22 g / l
SCJ-998B 10g / liter
SCJ-998C 5g / liter
(1) Domestic brand products should not only meet the standard requirements in the anti-mite anti-bacterial test, but also make the consumers feel the anti-mite, anti-bacterial, anti-odor, anti-mildew and anti-itch effects in the process of use, so it is recommended to use formula a.
(2) Products exported to the United States, Japan, Western Europe, and Australia are required to meet foreign standards when testing anti-mite and antibacterial effects, and formula b can meet their requirements.
3. Chemical operation: (for example, formula 100 liter solution according to formula a)
First add about 80 liters of water to the chemical tank, then add SCJ-998A 3.6Kg, stir, then add SCJ-998B 1.6Kg, then add SCJ-998C 0.8Kg, stir, (add appropriate amount of cationic or non-ionic softener) Finally, add water to 100 liters and mix well.
Third, high density fabric method
This method is derived from a plastic film, but the plastic film is not breathable and has a stuffy feel. The anti-mite effect is achieved by the high-density fabric itself, which is an isolation method. This method relies mainly on the weaving of the fabric itself or the microporous structure to prevent the infestation or penetration of the aphids, but it cannot repel or kill the aphids. If the sheets are made of such high-density fabrics, the mites on the sheets cannot enter the mattress under the sheets, but the mites can still survive by the secretions of the human body. For example, Tyvekò, which is exclusively produced by DuPont, is the material.
Tyvekò is a special fabric made of extremely fine high-density polyethylene (HDPE) fibers and produced by DuPont's original flash method. The monofilament of the Tyvek is about 0.5 micron, which is breathable, but it is impenetrable, including dust, liquid water, oil stains, dander, etc., which is invisible to the naked eye, but its diameter is much larger than 0.5 micron (the size of the locust body) At about 300 microns, the feces are between 10 and 40 microns, so it is not transparent. Similar materials include polytetrafluoroethylene laminated composite fabrics, coated fabrics, and the like. In addition to the physical isolation of aphids, these materials also have special properties such as dustproof, waterproof, chemical leakage, breathability, flexibility, and warmth.
Nowadays, in Europe and the United States, anti-mite fabrics have been adopted by many bedding and mattress manufacturers. In China, some excellent home textile companies are gradually adopting JLSUN® anti-mite textiles.
[China Antibacterial Fabric Network ]
ZeroClipboard.setMoviePath('/plugin/copytofriends/ZeroClipboard.swf'); var clip = new ZeroClipboard.Client(); clip.setHandCursor(true); clip.setText(" Development of anti-mite technology and anti-mite fabric http:/ /"); clip.addEventListener('complete', function(client,text){ alert("Successfully copy this article to the clipboard!"); }); clip.glue('copytofriends ');
Knit Print Hacci Top,Gauze Star Long Sleeve Top,Lace Collar Hacci Top,Hem Draw String Top
SHAOXING CHENYEE TEXTILE CO. LTD , https://www.fabriccy.com